Antriebstechnik für Dosiergeräte - optimale Dosierergebnisse durch perfekte Abstimmung
Dosiergeräte spielen in vielen Industriezweigen, darunter Chemie, Pharmazie, Lebensmittel- und Getränkeindustrie, eine entscheidende Rolle. Sie ermöglichen die genaue Zuführung von Flüssigkeiten, Pulvern oder Granulaten in Produktionsprozesse. Die Herzstücke dieser Systeme sind die Antriebstechnik und die zugehörige Steuerung, deren Auswahl und Auslegung maßgeblich die Effizienz, Präzision und Zuverlässigkeit der Dosierung bestimmen.
Antriebstechniken in Dosiergeräten reichen von elektrisch, pneumatisch bis hin zu hydraulisch. Jede Technik bietet spezifische Vorteile, abhängig von der Anwendung, wie z.B. Präzision bei der Dosierung geringster Mengen oder die Kraft für den Transport hochviskoser Medien. Die Steuerung dieser Antriebe, ob manuell, halbautomatisch oder vollautomatisch, ist entscheidend für die Integration des Dosiergeräts in Produktionsabläufe. Sie muss nicht nur präzise und zuverlässig arbeiten, sondern auch flexibel genug sein, um sich schnell an unterschiedliche Prozessanforderungen anpassen zu können.
Die Herausforderung bei der Entwicklung von Dosiergeräten liegt darin, Antriebstechnik und Steuerung so aufeinander abzustimmen, dass eine optimale Performance erreicht wird. Dies erfordert ein tiefes Verständnis sowohl der mechanischen als auch der softwaretechnischen Aspekte. Die richtige Kombination von Antriebs- und Steuerungstechnik ermöglicht es, Dosierprozesse effizient, präzise und mit hoher Wiederholgenauigkeit durchzuführen, was in der modernen Produktion unverzichtbar ist.
Antriebstechnik von DEMIC: Ihre Vorteile
Abgestimmte Komplettlösung
Steuerungstechniken und Antriebstechnik sind perfekt aufeinander abgestimmt um optimale Dosierergebnisse zu erzielen.
Single Point of Power
Einheitliche Spannungsversorgung an einer Stelle für das gesamte Dosiergerät.
Frequenzumrichtertechnik
Optimierte Prozesssteuerung durch präzise Geschwindigkeitsregelung von Motoren.
2 Motoren
Aufeinander abstimmbare Förderung und Produktaktivierung für gleichmäßigen Produktfluss.
Grundlagen der Antriebstechnik für Dosiergeräte
Was versteht man unter Antriebstechnik?
Antriebstechnik bezieht sich auf die Methoden und Geräte, die zur Bewegung oder Steuerung einer Maschine oder eines ihrer Teile verwendet werden. In der Technologie der Dosiergeräte umfasst sie die Systeme und Komponenten, die notwendig sind, um Materialien präzise und kontrolliert zuzuführen. Dies kann elektrische Motoren, pneumatische Systeme oder hydraulische Pumpen einschließen. Die Auswahl des Antriebssystems hängt von mehreren Faktoren ab, darunter die Art des zu dosierenden Materials, die erforderliche Präzision und die Umgebungsbedingungen. Elektrische Antriebe bieten beispielsweise eine exzellente Steuerbarkeit für kleine bis mittlere Durchflussmengen, während pneumatische oder hydraulische Systeme oft bei größeren Volumen oder bei Materialien, die einen höheren Druck benötigen, zum Einsatz kommen.
Die Rolle der Antriebstechnik in Dosiergeräten
Die Antriebstechnik ist entscheidend für die Funktionalität von Dosiergeräten, da sie die Grundlage für die Präzision und Wiederholbarkeit der Dosierprozesse bildet. Ein effektives Antriebssystem ermöglicht es, exakte Mengen an Materialien in einem kontrollierten Tempo zuzuführen, was essentiell ist, um die Konsistenz und Qualität der Endprodukte zu gewährleisten. In der Pharmazie, wo genaue Dosierungen lebensnotwendig sein können, oder in der Lebensmittelproduktion, wo die Einhaltung von Rezepturen kritisch ist, spielt die Präzision der Antriebstechnik eine übergeordnete Rolle. Darüber hinaus beeinflusst die Antriebstechnik die Effizienz des gesamten Systems, indem sie den Energieverbrauch optimiert und die Wartungsanforderungen minimiert.
Unterschied zwischen Antriebs- und Steuerungstechnik
Obwohl Antriebs- und Steuerungstechnik eng miteinander verbunden sind, dienen sie unterschiedlichen Zwecken in Dosiergeräten. Die Antriebstechnik ist primär für die mechanische Bewegung zuständig, also das tatsächliche Aktivieren und Bewegen der Komponenten, die die Materialien dosieren. Die Steuerungstechnik hingegen umfasst die elektronischen oder softwarebasierten Systeme, die diese Bewegungen regeln und koordinieren. Sie sorgt dafür, dass der Antrieb zur richtigen Zeit, in der richtigen Menge und am richtigen Ort aktiviert wird. Steuerungssysteme können von einfachen manuellen Einstellungen bis hin zu hochkomplexen, vollautomatisierten Interfaces reichen, die in der Lage sind, sich selbst anzupassen und zu optimieren, basierend auf Feedback von den Produktionsprozessen. Diese Unterscheidung ist entscheidend, um effiziente und präzise Dosierprozesse in industriellen Anwendungen zu gewährleisten.
Arten von Antrieben für Dosiergeräte
Die Antriebstechniken für Dosiergeräte lassen sich hauptsächlich in drei Kategorien einteilen: elektrisch, pneumatisch und hydraulisch. Jede Technologie besitzt spezifische Eigenschaften, die sie für bestimmte Anwendungsgebiete prädestinieren.
Elektrische Antriebe
Diese zeichnen sich durch Präzision, Energieeffizienz und einfache Steuerbarkeit aus. Ideal für hochgenaue Dosierungen, ermöglichen sie eine saubere und leise Betriebsweise. Spezifisch:
- Schrittmotoren sind für feine Positionierung ohne Feedback ideal, besonders in präzisen, kleinvolumigen Dosieraufgaben.
- Servomotoren bieten durch Feedback-Systeme hohe Kontrolle bei dynamischen Dosieranwendungen.
- Drehstrommotoren eignen sich für robuste industrielle Einsätze, insbesondere bei der Dosierung größerer oder viskoserer Mengen.
Pneumatische Antriebe
nutzen komprimierte Luft, um Bewegung zu erzeugen. Diese Antriebe sind besonders robust gegenüber schmutzigen oder gefährlichen Umgebungen und sicher in explosionsgefährdeten Bereichen einsetzbar. Sie bieten Einfachheit und Zuverlässigkeit, da sie mit wenigen beweglichen Teilen auskommen und leicht zu warten sind. Ihre Sicherheit bei feuergefährlichen Materialien resultiert aus der Funkenfreiheit während des Betriebs. Obwohl kostengünstiger in der Anschaffung als komplexe elektrische Systeme, bieten sie im Vergleich eine geringere Präzision. Ihre schnelle und kraftvolle Bewegungsfähigkeit macht sie ideal für Anwendungen, die weniger Feinheit, aber hohe Reaktionsgeschwindigkeit und Robustheit erfordern.
Hydraulische Antriebe
nutzen Flüssigkeiten unter hohem Druck, um große Kräfte zu erzeugen, was sie ideal für schwere Lasten und Hochdruckanwendungen macht. Sie sind in der Schwerindustrie weit verbreitet, wo große Mengen an Materialien bewegt oder dosiert werden müssen. Diese Antriebe zeichnen sich durch ihre Fähigkeit aus, erhebliche Lasten zu bewältigen, was sie für anspruchsvolle industrielle Aufgaben besonders geeignet macht. Allerdings erfordern hydraulische Systeme eine komplexere Wartung und verbrauchen mehr Energie im Vergleich zu anderen Antriebstypen. Trotz dieser Nachteile bieten sie eine zuverlässige und effektive Lösung für viele industrielle Herausforderungen, bei denen es auf maximale Kraftanwendung ankommt.
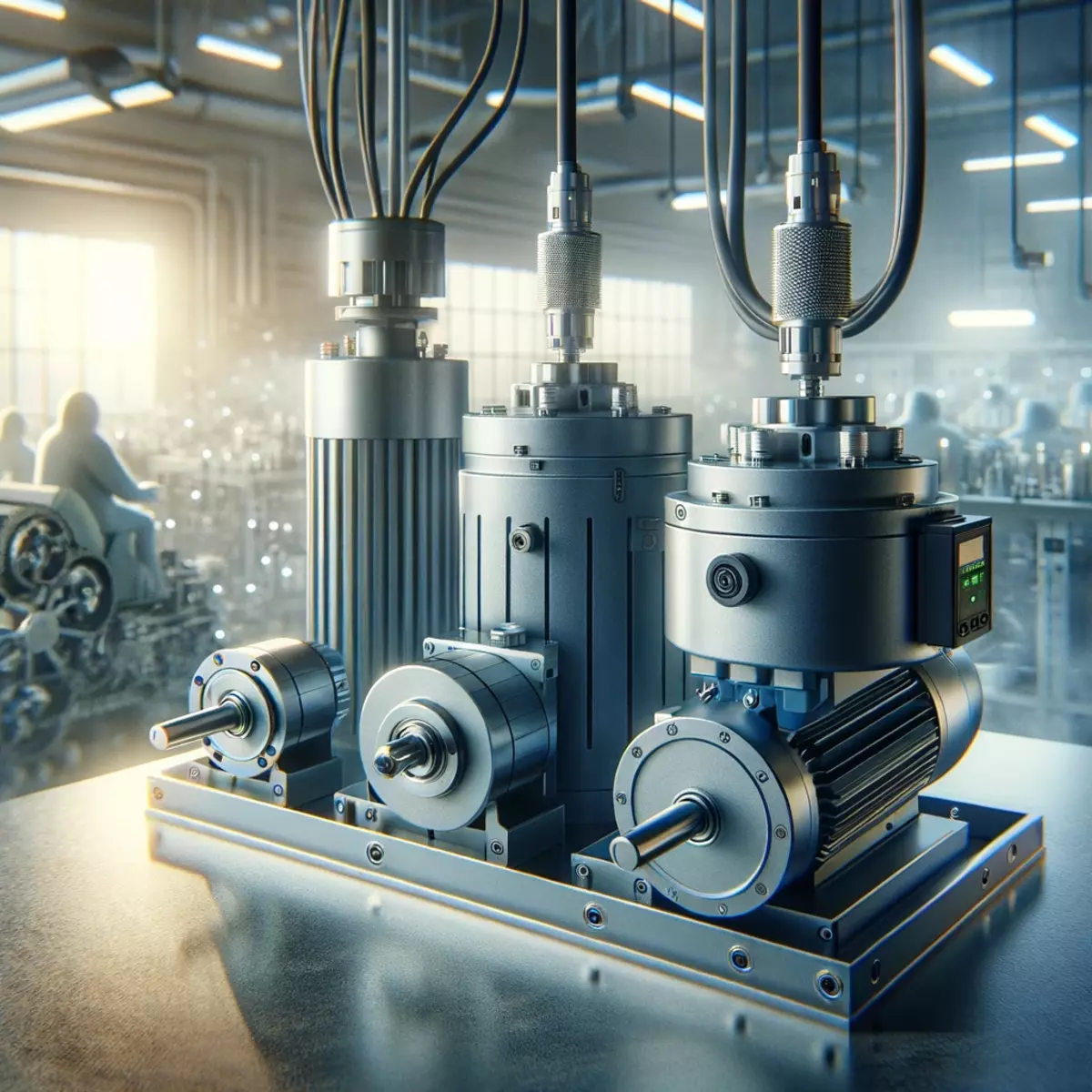
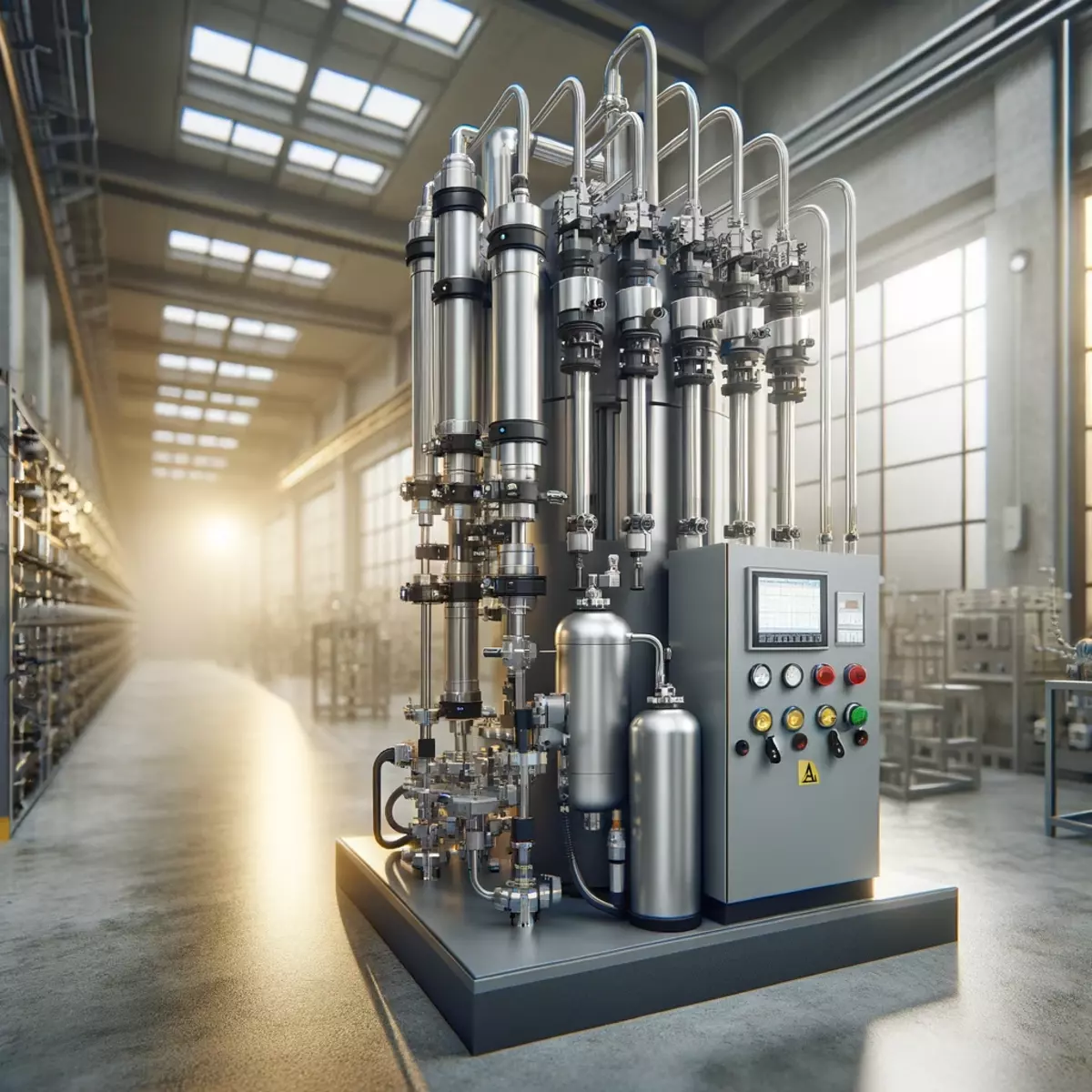
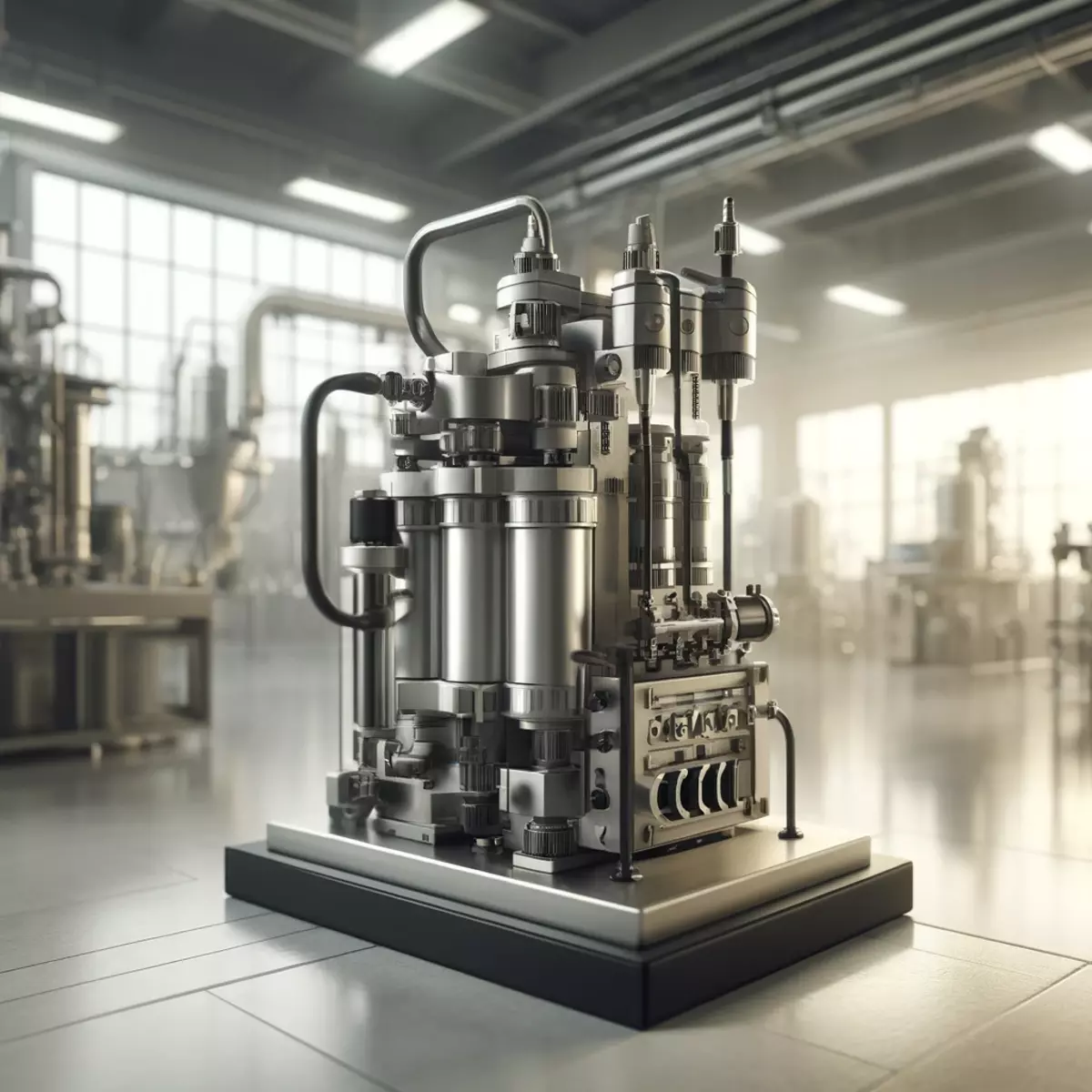
Die Auswahl der geeigneten Antriebstechnik hängt somit stark von den spezifischen Anforderungen der Dosieraufgabe, wie Präzision, Last, Umgebungsbedingungen und Effizienz ab.
Frequenzumrichter - Effiziente Steuerung von Antriebsmotoren
Was sind Frequenzumrichter und wie funktionieren sie?
Frequenzumrichter sind elektronische Geräte, die die Drehzahl eines Elektromotors steuern, indem sie die Frequenz des an den Motor gelieferten Stroms variieren. Sie wandeln den eingehenden Wechselstrom in Gleichstrom um und erzeugen daraus einen Ausgangswechselstrom variabler Frequenz.
Durch die Änderung dieser Frequenz können Frequenzumrichter die Geschwindigkeit von Motoren präzise steuern. Diese Fähigkeit, die Motorleistung exakt zu regulieren, macht sie besonders wertvoll in Anwendungen, wo Prozessoptimierung und Energieeffizienz kritisch sind.
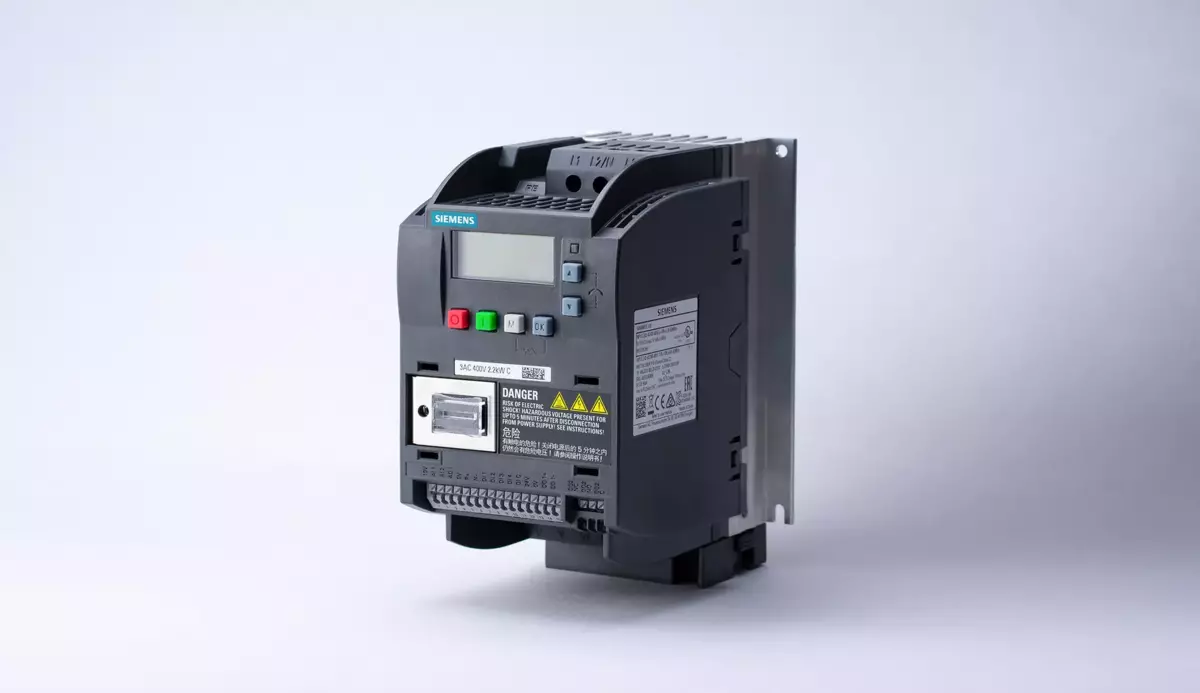
Vorteile von Frequenzumrichtern in der Antriebstechnologie
Frequenzumrichter bieten bedeutende Vorteile in der Antriebstechnologie. Ihre Fähigkeit, die Motorleistung präzise zu steuern, führt zu einer verbesserten Prozesseffizienz und Energieeinsparung, da Motoren nur so viel Energie verbrauchen, wie sie für die jeweilige Aufgabe benötigen. Dies reduziert nicht nur die Betriebskosten,
sondern trägt auch zur Verlängerung der Lebensdauer der Motoren bei, indem mechanische Belastungen und Überhitzungsrisiken minimiert werden. Zudem ermöglichen sie eine sanfte Anlauf- und Auslaufphase, was die mechanische Beanspruchung des Antriebssystems weiter reduziert.
Anpassung der Motordrehzahl mit Frequenzumrichtern
Die Anpassung der Motordrehzahl ist eine der Hauptfunktionen von Frequenzumrichtern. Durch die Veränderung der Frequenz des an den Motor gelieferten Stroms können Anwender die Geschwindigkeit des Motors flexibel steuern. Dies ist besonders vorteilhaft in Produktionsumgebungen, wo unterschiedliche Materialien oder Bearbeitungsschritte unterschiedliche Geschwindigkeiten erfordern.
Die Möglichkeit, die Drehzahl genau einzustellen, ermöglicht eine optimale Anpassung an die jeweiligen Prozessanforderungen, was die Effizienz steigert und die Produktqualität verbessert. Frequenzumrichter sind daher essenzielle Komponenten in modernen Automatisierungs- und Steuerungssystemen.
Integration von Frequenzumrichtern für optimale Dosierergebnisse
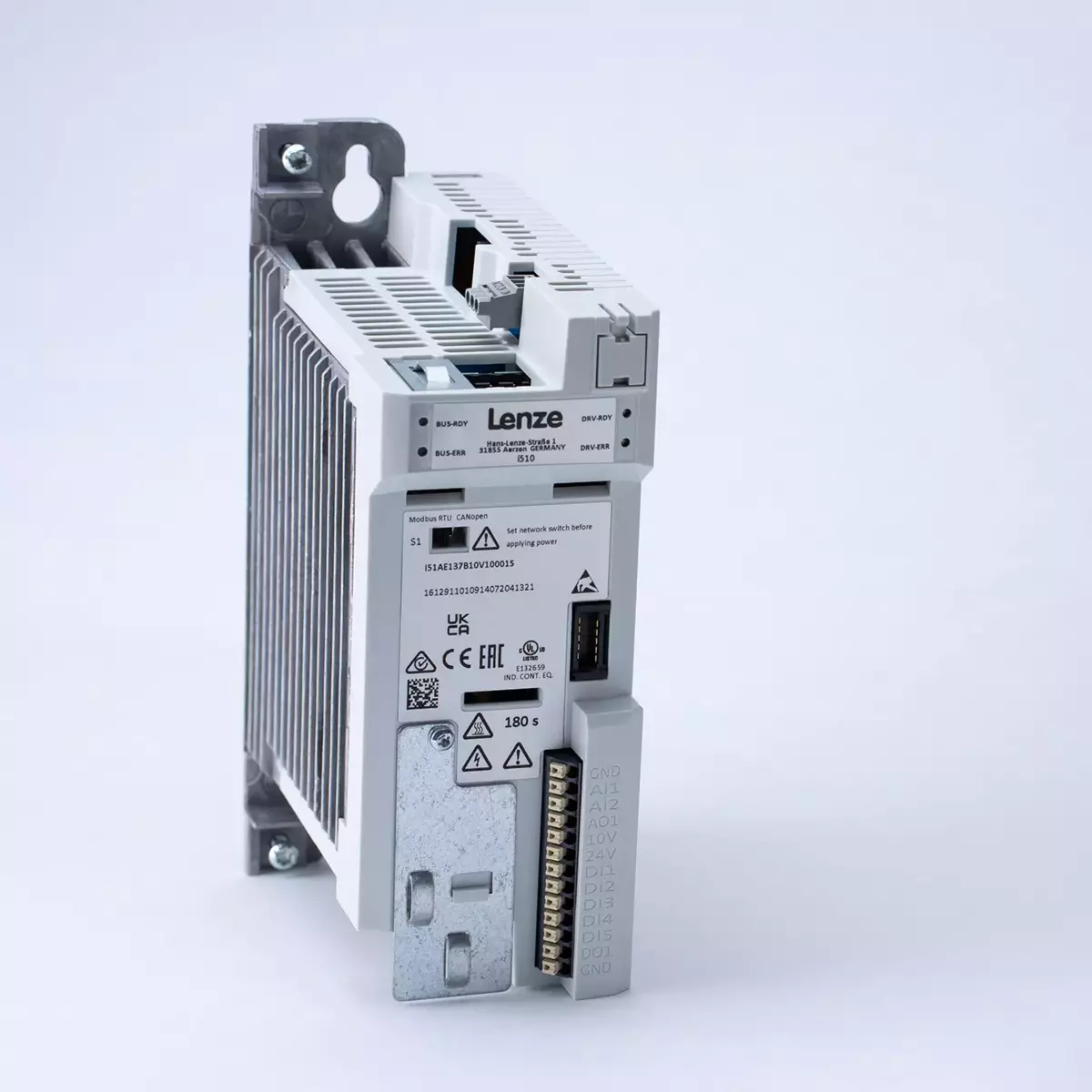
Herausforderungen bei der Implementierung von Frequenzumrichtern
Die Einführung von Frequenzumrichtern in bestehende Systeme kann technische und organisatorische Herausforderungen mit sich bringen. Technisch erfordert die Installation eine genaue Abstimmung zwischen dem Frequenzumrichter und den Motorcharakteristika, um Effizienzverluste und mögliche Schäden zu vermeiden. Organisatorisch kann die Schulung des Personals für den Umgang mit dieser Technologie eine Herausforderung darstellen, da ein tiefes Verständnis für die Funktionsweise und die Programmierung der Geräte erforderlich ist. Zudem müssen bestehende Prozesse häufig angepasst oder neu konfiguriert werden, um die Vorteile der präzisen Drehzahlsteuerung voll ausschöpfen zu können.
Synchronisation von Frequenzumrichter und Steuerungstechnik
Die Synchronisation von Frequenzumrichtern mit der Steuerungstechnik ist entscheidend für eine effiziente und präzise Prozesssteuerung. Eine gute Abstimmung ermöglicht es, dass der Frequenzumrichter reibungslos auf Steuersignale reagiert und die Motorleistung präzise an die Anforderungen des Prozesses anpasst. Dies erfordert eine sorgfältige Programmierung und oft auch die Integration von Feedback-Systemen, die Echtzeitdaten über die Motorleistung und die Prozessparameter liefern. Diese Daten helfen bei der Feinjustierung der Frequenzumrichter-Einstellungen, um eine optimale Abstimmung und damit verbesserte Produktqualität und Prozesseffizienz zu erreichen.
Auswahl des passenden Frequenzumrichters
Faktoren für die Auswahl eines Frequenzumrichters für Dosiergeräte
Bei der Auswahl des geeigneten Frequenzumrichters für Dosiergeräte sind verschiedene Schlüsselfaktoren zu berücksichtigen:
- Motorleistung: Die Leistungsanforderungen des Motors müssen genau mit den Spezifikationen des Frequenzumrichters übereinstimmen.
- Betriebsbedingungen: Art des Materials, das dosiert wird, sowie die erforderliche Präzision und Wiederholbarkeit der Dosierung sind entscheidend.
- Umgebungsbedingungen: Die Geräte müssen für die spezifischen Umgebungsbedingungen geeignet sein, einschließlich Temperatur, Feuchtigkeit und möglicher Exposition gegenüber Chemikalien oder Staub.
- Betriebssicherheit und -effizienz: Die Auswahl muss sowohl die Betriebssicherheit als auch die Energieeffizienz maximieren, um die Betriebskosten zu minimieren.
Diese Faktoren helfen dabei, einen Frequenzumrichter auszuwählen, der optimal auf die spezifischen Anforderungen und Bedingungen abgestimmt ist.
Individuelle Beratung durch DEMIC Datentechnik GmbH
DEMIC Datentechnik GmbH bietet individuelle Beratungsdienstleistungen an, um Unternehmen bei der Auswahl des optimalen Frequenzumrichters für ihre spezifischen Dosieranwendungen zu unterstützen. Die Experten von DEMIC berücksichtigen alle relevanten Faktoren, wie die technischen Spezifikationen der Dosiergeräte, die chemischen Eigenschaften der zu dosierenden Materialien und die Umgebungsbedingungen. Durch diese maßgeschneiderte Beratung stellt DEMIC sicher, dass die Kunden einen Frequenzumrichter erhalten, der nicht nur technisch kompatibel ist, sondern auch die höchstmögliche Effizienz und Zuverlässigkeit in ihren spezifischen Anwendungsfällen bietet.
Best Practices für die Einrichtung und Wartung von Frequenzumrichtern
Installation von Frequenzumrichtern – Woran Sie denken sollten
Bei der Installation von Frequenzumrichtern gibt es mehrere wichtige Punkte zu beachten:
- Standortwahl: Wählen Sie einen Standort mit ausreichender Belüftung und Schutz vor extremen Temperaturen und Feuchtigkeit.
- Elektrische Sicherheit: Stellen Sie sicher, dass alle elektrischen Verbindungen korrekt und sicher sind, um elektrische Sicherheitsrisiken zu minimieren.
- Kompatibilität: Überprüfen Sie die Kompatibilität des Frequenzumrichters mit den zu steuernden Motoren und anderen Systemkomponenten.
- Inbetriebnahme: Führen Sie nach der Installation eine gründliche Inbetriebnahme durch, um sicherzustellen, dass alle Systeme korrekt funktionieren und effizient eingestellt sind.
Diese Vorbereitungen tragen dazu bei, dass der Frequenzumrichter optimal funktioniert und potenzielle Probleme frühzeitig erkannt werden.
Wartung von Frequenzumrichtern zur Verlängerung der Lebensdauer
Regelmäßige Wartung ist entscheidend, um die Lebensdauer von Frequenzumrichtern zu verlängern und deren Leistungsfähigkeit zu erhalten:
- Regelmäßige Inspektionen: Überprüfen Sie regelmäßig alle elektrischen und mechanischen Komponenten auf Verschleiß oder Beschädigung.
- Software-Updates: Führen Sie Software-Updates durch, um sicherzustellen, dass der Frequenzumrichter mit der neuesten Technologie arbeitet und optimale Leistung bietet.
- Reinigung: Halten Sie den Frequenzumrichter und seine Umgebung sauber, um eine Überhitzung und Ansammlung von Staub zu vermeiden, die die Leistung beeinträchtigen könnten.
- Dokumentation: Halten Sie detaillierte Aufzeichnungen über alle Wartungsaktivitäten und eventuelle Probleme, um zukünftige Wartungen zu erleichtern und eine kontinuierliche Leistung zu gewährleisten.
Diese Wartungspraktiken helfen dabei, Ausfälle zu minimieren und die Zuverlässigkeit des Frequenzumrichters über seine gesamte Lebensdauer hinweg sicherzustellen.
Steuerungstechnik - Das Gehirn der Antriebstechnik
Bedeutung der Steuerung für präzise Dosierung
Die Steuerungstechnik spielt eine zentrale Rolle in der Dosierungstechnik, indem sie die Präzision und Zuverlässigkeit der Prozesse gewährleistet. Sie ermöglicht es, die Menge, Geschwindigkeit und Timing der zugeführten Materialien genau zu regeln. Dies ist besonders wichtig in Branchen wie der Pharmazie und Chemie, wo präzise Dosierungen entscheidend für die Produktqualität und Sicherheit sind. Durch fortgeschrittene Steuerungsmechanismen können Dosiergeräte auch unter variierenden Umgebungsbedingungen und Materialbeschaffenheiten konsistente Ergebnisse liefern.
Arten von Steuerungen für Dosiergeräte
Die Auswahl der Steuerung hängt von den spezifischen Anforderungen der Anwendung, der Komplexität der Prozesse und dem gewünschten Automatisierungsgrad ab.
Manuelle Steuerungen
Manuelle Steuerungen erfordern direktes menschliches Eingreifen, um die Dosiergeräte zu bedienen. Sie sind einfach in der Handhabung und oft kostengünstig in der Anschaffung. Diese Art der Steuerung eignet sich für kleinere oder weniger komplexe Operationen, wo einfache Anpassungen ausreichend sind und keine hohen Anforderungen an die Präzision gestellt werden.
Programmierbare Logikcontroller (PLCs)
PLCs sind robuste und zuverlässige elektronische Geräte, die speziell dafür entwickelt wurden, eine Vielzahl von industriellen Steuerungs- und Automatisierungsaufgaben zu übernehmen. Sie sind programmierbar, was bedeutet, dass sie flexibel an unterschiedliche Betriebsbedingungen und Anforderungen angepasst werden können. PLCs sind ideal für komplexe Dosiersysteme, die eine schnelle Verarbeitung von Signalen und eine präzise Steuerung benötigen.
Computerbasierte Steuerungssysteme
Computerbasierte Steuerungssysteme bieten die höchste Flexibilität und Präzision für die Dosierungstechnik. Sie nutzen fortschrittliche Software, die komplexe Algorithmen und Prozesssteuerungen ermöglicht. Diese Systeme können leicht an sich ändernde Parameter angepasst werden und bieten umfangreiche Diagnose- und Überwachungsfunktionen, was sie besonders geeignet für hochautomatisierte und präzisionskritische Anwendungen macht.
Synchronisierung von Antriebs- und Steuerungstechnik
Warum ist die Abstimmung essentiell?
Die Abstimmung zwischen Antriebs- und Steuerungstechnik ist entscheidend, um die Effizienz und Genauigkeit von Dosierprozessen zu maximieren. Eine korrekte Synchronisation stellt sicher, dass die Antriebssysteme präzise auf die Befehle der Steuerungstechnik reagieren, was zu einer verbesserten Produktqualität,
geringeren Materialverschwendung und einer höheren Gesamtanlagenzuverlässigkeit führt. Ohne diese Harmonisierung können Inkonsistenzen und Fehler auftreten, die die Leistung und Sicherheit des Systems beeinträchtigen.
Herausforderungen bei der Synchronisation
Die Synchronisation von Antriebs- und Steuerungstechnik bringt mehrere Herausforderungen mit sich. Dazu zählen die Integration von Hardware mit unterschiedlichen Schnittstellen und die Abstimmung von Softwareprotokollen, die oft von verschiedenen Herstellern stammen. Des Weiteren erfordert die Echtzeitkommunikation
zwischen Antrieb und Steuerung hochpräzise Timing-Mechanismen, um Verzögerungen und Fehler in der Signalverarbeitung zu vermeiden. Diese technischen Anforderungen können die Einrichtung und Inbetriebnahme komplex und kostspielig machen.
Best Practices für die optimale Abstimmung
Um eine optimale Abstimmung zwischen Antriebs- und Steuerungstechnik zu erreichen, sollten folgende Best Practices beachtet werden: Erstens ist die Verwendung von standardisierten und kompatiblen Komponenten empfehlenswert, um die Integration zu erleichtern. Zweitens sollte eine gründliche Planung und Simulation
der Systeme vor der eigentlichen Implementierung erfolgen, um potenzielle Probleme frühzeitig zu identifizieren. Schließlich ist regelmäßiges Training des Bedienpersonals wichtig, um sicherzustellen, dass alle Beteiligten verstehen, wie die Systeme zusammenarbeiten und wie eventuelle Störungen effizient behoben werden können.
Auswahl der richtigen Antriebstechnik
Anforderungen definieren
Vor der Auswahl der richtigen Antriebstechnik für Dosiergeräte ist es entscheidend, die spezifischen Anforderungen des Dosierprozesses klar zu definieren. Dies umfasst das Verstehen der Materialart, die dosiert werden soll, die erforderliche Präzision, die Durchsatzrate und Umgebungsbedingungen wie Temperatur oder potenzielle Explosionsgefahr. Ebenso sind die Betriebskosten und Wartungsanforderungen zu berücksichtigen. Eine präzise Definition dieser Parameter hilft dabei, eine Antriebstechnik zu wählen, die optimale Leistung und Effizienz im geplanten Anwendungsbereich gewährleistet.
Auswahlkriterien für Dosiergeräte-Antriebe
Die Auswahl des passenden Antriebs für Dosiergeräte basiert auf mehreren Kriterien. Zu den wichtigsten gehören die Art des Antriebs (elektrisch, pneumatisch, hydraulisch), die Energieeffizienz, die Steuerbarkeit, die Skalierbarkeit und die Integrationsfähigkeit in bestehende Systeme. Auch die Betriebssicherheit spielt eine wesentliche Rolle, insbesondere in regulierten Branchen wie der Pharmazie und Chemie. Die Fähigkeit, präzise und reproduzierbar zu dosieren sowie eine schnelle Anpassung an veränderte Produktionsbedingungen, sind ebenfalls entscheidend für die Auswahl.
Warum eine fachkundige Beratung wichtig ist
Die Auswahl der richtigen Antriebstechnik kann komplex sein, insbesondere in spezialisierten oder hochtechnisierten Anwendungen. Fachkundige Beratung ist daher unerlässlich, um teure Fehlentscheidungen zu vermeiden und die Investitionen zu sichern. Experten können nicht nur dabei helfen, die technischen Anforderungen präzise zu definieren, sondern auch die neuesten Technologien und Lösungen vorschlagen, die speziell auf die Bedürfnisse des jeweiligen Produktionsprozesses zugeschnitten sind. Durch ihre Erfahrung und ihr Fachwissen unterstützen sie Unternehmen dabei, die Betriebseffizienz zu maximieren und die Einhaltung von Branchenstandards und Sicherheitsvorschriften zu gewährleisten.
Wartung und Instandhaltung von Antriebstechnik
Regelmäßige Wartungsintervalle
Die Festlegung von regelmäßigen Wartungsintervallen ist entscheidend für die Langlebigkeit und Effizienz der Antriebstechnik in Dosiergeräten. Es empfiehlt sich, Wartungspläne zu erstellen, die auf den Empfehlungen der Hersteller basieren und zusätzlich die spezifischen Betriebsbedingungen berücksichtigen. Regelmäßige Wartungen sollten Inspektionen, Reinigungsarbeiten, Schmierungen, sowie die Überprüfung und den Austausch von Verschleißteilen umfassen. Auch die Überwachung der Systemleistung und eventuelle Software-Aktualisierungen sind wichtig. Diese Maßnahmen helfen, die Betriebssicherheit zu erhöhen, die Leistungsfähigkeit der Geräte zu erhalten und unerwartete Ausfälle zu vermeiden. Ein gut geplanter Wartungszyklus trägt wesentlich dazu bei, die Gesamtbetriebskosten zu senken und die Produktivität zu steigern.
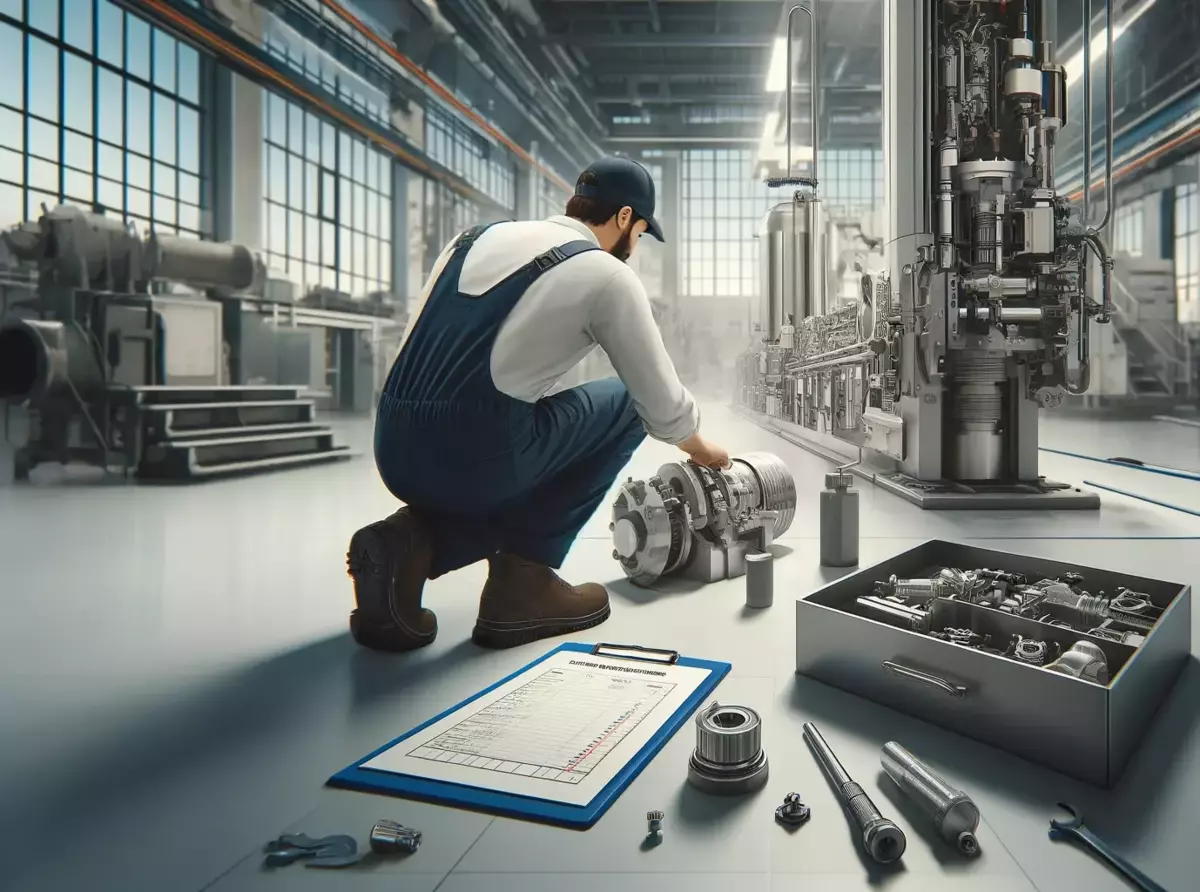
Vorbeugende Instandhaltungsstrategien
Vorbeugende Instandhaltung spielt eine entscheidende Rolle bei der Minimierung von Betriebsunterbrechungen und der Verlängerung der Lebensdauer von Antriebssystemen. Diese Strategie basiert auf der regelmäßigen Überprüfung und Wartung der Ausrüstung, um Probleme zu identifizieren und zu beheben, bevor sie zu schwerwiegenden Fehlern führen. Moderne Überwachungstechnologien, wie Vibrationssensoren und Thermografie, werden eingesetzt, um Anzeichen von Abnutzung oder Fehlfunktionen frühzeitig zu erkennen. Ein proaktiver Ansatz in der Instandhaltung ermöglicht es, geplante Wartungen durchzuführen, die weniger invasiv und kostengünstiger sind als reaktive Reparaturen nach einem Ausfall. Effektive vorbeugende Instandhaltungspläne berücksichtigen die Betriebsbedingungen der Antriebe und sind auf eine optimale Leistung und lange Lebensdauer der Antriebstechnik ausgerichtet.
Zukunft der Antriebstechnik in Dosiergeräten
Innovative Entwicklungen
Die Zukunft der Antriebstechnik in Dosiergeräten wird stark von Innovationen geprägt, die Effizienz, Präzision und Anpassungsfähigkeit erhöhen. Zu den bemerkenswerten Entwicklungen gehören der Einsatz von smarten Motoren, die mit integrierter Sensorik ausgestattet sind, um Betriebsdaten in Echtzeit zu erfassen und selbstständig Anpassungen vorzunehmen. Diese intelligenten Antriebssysteme ermöglichen eine präzisere Steuerung und Diagnostik, was die Wartung vereinfacht und die Betriebssicherheit erhöht. Weiterhin wird die Integration von künstlicher Intelligenz zur Vorhersage von Wartungsbedürfnissen und zur Optimierung der Dosierprozesse eine immer wichtigere Rolle spielen.
Trends in der Antriebs- und Steuerungstechnik
Aktuelle Trends in der Antriebs- und Steuerungstechnik für Dosiergeräte zeigen eine klare Bewegung hin zur weiteren Automatisierung und Digitalisierung. Die Vernetzung von Antriebssystemen über das Internet der Dinge (IoT) ermöglicht eine verbesserte Datensammlung und -analyse, die für präzisere Steuerungsentscheidungen genutzt wird. Zudem wird die Entwicklung energiesparender und umweltfreundlicher Technologien vorangetrieben, um Nachhaltigkeitsziele zu unterstützen. Diese Trends deuten auf eine Zukunft hin, in der Antriebs- und Steuerungssysteme zunehmend komplexer, jedoch auch effizienter, anpassungsfähiger und benutzerfreundlicher werden.
FAQs zu Antriebstechnik
Elektrische Antriebe bieten hohe Präzision, Energieeffizienz und einfache Steuerbarkeit. Sie sind ideal für Anwendungen, die eine hohe Genauigkeit und Wiederholbarkeit erfordern und eignen sich besonders gut für saubere, leise Betriebsbedingungen wie in Laboren oder Reinräumen.
Pneumatische Antriebe sind besonders geeignet für Umgebungen, die robuste und sichere Lösungen erfordern, wie z.B. in explosiven oder sehr schmutzigen Umgebungen. Sie sind ideal für Anwendungen, die schnelle und kraftvolle Bewegungen benötigen.
Zu den Herausforderungen gehören die Integration in bestehende Systeme, die Kompatibilität mit bestehenden Motoren und die Schulung des Bedienpersonals. Zudem kann die Echtzeitkommunikation zwischen Antrieb und Steuerung technisch anspruchsvoll sein.
Eine gute Synchronisation verbessert die Effizienz und Genauigkeit der Prozesse, minimiert Materialverschwendung und erhöht die Zuverlässigkeit des gesamten Systems. Sie ist essentiell für die Optimierung der Produktionsabläufe und die Qualität der Endprodukte.
Wichtige Faktoren sind die Leistungsanforderungen des Motors, die spezifischen Betriebsbedingungen, die Art des zu dosierenden Materials und die erforderliche Präzision. Auch Umweltbedingungen und Sicherheitsanforderungen spielen eine Rolle.
Eine vorbeugende Wartungsstrategie beinhaltet regelmäßige Inspektionen, den Austausch von Verschleißteilen, Software-Updates und die Überwachung durch moderne Diagnosetechnologien, um Probleme frühzeitig zu erkennen und zu beheben.
Durch regelmäßige Wartung, einschließlich der Reinigung und Überprüfung aller Teile auf Verschleiß und Schäden, sowie durch die Anwendung vorbeugender Wartungspraktiken kann die Lebensdauer von Antriebstechnik signifikant verlängert werden.
Neue Trends beinhalten die zunehmende Automatisierung, die Integration von IoT für verbesserte Datenanalyse und Fernüberwachung sowie die Entwicklung energieeffizienter und umweltfreundlicher Technologien, um Nachhaltigkeitsziele zu erreichen.
Möchten Sie mehr über Antriebstechnik für Dosiergeräte erfahren?
Wir freuen uns darauf, Sie zu beraten:
TELEFON: +49 2247 918 90
E-MAIL: kontakt(at)demic-datentechnik.de
Oder schicken Sie uns eine Nachricht: